How to go-to-market: three case studies
- Pippa Gawley
- 2 days ago
- 10 min read
Updated: 5 hours ago
Bringing a physical product from concept to customer involves a critical strategic decision: how exactly will it be manufactured? There are many potential answers and the correct path for you may well involve several of them, and the combinations will also change over time.
Companies face a choice between leveraging the scale and expertise of established contract manufacturers; forging deeper, more integrated strategic partnerships; or taking the bold step of building their own production capabilities, often requiring the development of a "first-of-a-kind" (FOAK) plant for novel technologies. As they scale, the FOAK route may keep things in-house, building next-of-a-kinds (NOAKs), or keep the FOAK as a demo and licence the technology to partners. This decision is not straightforward and hinges on a complex interplay of factors. Key considerations include the maturity and uniqueness of the product's technology, the capital investment required versus available funding, the desired level of control over quality and intellectual property, projected production volumes and scalability needs, speed-to-market pressures, and the company's core competencies and long-term strategic vision. Ultimately, the level of vertical integration (ie the more of the processing/manufacturing steps you do yourself) is likely to determine how much of the value creation you can capture, so it will be of interest to your backers from the start. To give some colour about how different companies have navigated these choices, we will explore the different manufacturing strategies adopted by three companies from Pippa's angel portfolio in the US: CleanFiber, Gradient, and Lilac Solutions. Each offers valuable lessons on aligning production approaches with specific business goals and technological realities.
Case study 1: CleanFiber - Transforming recycled cardboard into sustainable building insulation (FOAK route)
How It Started
CleanFiber was founded in Buffalo, New York, in 2013 by CEO Jonathan Strimling with co-founders who were veteran cellulose installers. They realised that the primary feedstock for cellulose insulation—newsprint—was in terminal decline, and they had the idea of creating high-performance cellulose insulation from recycled corrugated cardboard. This new approach not only addressed the environmental concerns associated with traditional insulation materials which use petrochemical feedstocks, but also provided a sustainable solution to the growing issue of cardboard waste. Pippa met Jonathan at a pitch event for impact angel group Investor’s Circle in San Francisco in September 2016, and made an angel investment in CleanFiber shortly afterwards.
How It’s Going

CleanFiber’s insulation is designed to provide superior coverage with less contamination and less dust compared to other cellulose insulation. The company utilises a liquid-based process to float off contaminants from the cardboard feedstock and infuse the cellulose fibers with fire retardant, resulting in a cleaner product with excellent thermal performance. This wet chemical process also ensures that the insulation meets rigorous fire safety standards, with an all-borate formulation proven to limit smouldering and flame propagation.
In 2024, CleanFiber was named the fastest growing manufacturing company in the US by Inc. 5000, achieving a three-year growth rate of 5,684%.
How they’ve scaled their production
CleanFiber knew from the start that they would need to build their own production facilities, as the machines making traditional cellulose insulation are designed to work with wood as an input. They wouldn't be able to produce insulation from cardboard, or to apply the fire retardant uniformly. So, CleanFiber built a series of progressively larger prototypes to derisk the product technically, followed by a demo unit to big enough to produce consistent samples for customers and service early sales. Once customer demand had been demonstrated, they progressed to a full-scale FOAK plant production facility in Buffalo. It started commercial production in 2020, and it is currently ramping up to produce over 3 million bags of insulation annually. This high production capacity will allow CleanFiber to offer its all-borate product at extremely competitive pricing. So far, they’ve shipped over 4 million bags (3,500 truckloads) from their facility in Buffalo and estimate their insulation is installed in approximately 30,000 family homes.

How They Funded Their Growth
CleanFiber has raised over $100M of total funding to support its growth and expansion. Initially, it raised mostly equity financing from aligned angel investors like Seattle-based E8, climate investors such as Clean Energy Ventures and circular economy specialists Closed Loop Partners, and regional investors like 43North. As they started to scale production, CleanFiber added in debt financing from a few providers, and their latest rounds have been a blended finance combination of equity, debt and grants. In 2022, the company secured $14 million in debt financing from Lapis Advisers to expand its Buffalo production facility. In 2023-4 they raised a total of $33M in Series B equity financing led by Spring Lane Capital joined by AXA Investment Managers and Climate Innovation Capital, supplemented with an additional $31.5M project financing facility and two $10M grants from the Department of Energy’s Office of Manufacturing and Energy Supply Chains. This financing allowed them to complete their FOAK and start construction of new production facilities, and roll out their product nationally.
Want to learn more about CleanFiber? They have been covered by TechCrunch, and you can follow them on LinkedIn.
Case study 2: Gradient - Revolutionizing HVAC (Partnerships route)
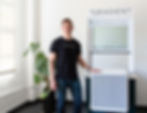
How It Started
Gradient was founded in 2017 by Vince Romanin, a mechanical engineer with a Ph.D. from the University of California, Berkeley. Romanin, a self-described “thermo-nerd,” developed a passion for thermodynamics and heat transfer during his academic career. Recognising the environmental impact of traditional HVAC systems, he created Gradient, with the mission to build products that are both good for the planet and at maintaining comfortable indoor environments. Pippa met Vince through the PRIME Impact Fund, who were early backers of Gradient, and made an angel investment in 2018.
How It’s Going
The core technology of Gradient is a super efficient heat pump, which uses less than half the energy of a standard heating system and window A/C, and takes up far less of the window. It looks great, and is designed for easy installation. It performs both heating and cooling, operates quietly, and uses the more environmentally-friendly refrigerant R32. Because it doesn’t need professional installation, the total cost is around half that of a typical heat pump at around $3,800.

In 2022, Gradient won the New York City Housing Authority Clean Heat for All Challenge which led to an order for 10,000 units (video). This started with a 37-unit pilot in NYCHA apartments in November 2023. The installations were completed efficiently, with each unit taking approximately 20 minutes to install. Residents loved their performance, improved air quality, and how quiet they were. Gradient’s partnership with NYCHA has allowed for constant improvement of the product through customer feedback, and has led to developments like the novel ‘meltwater atomiser’ designed to fix the problem of water dripping onto cold sidewalks and freezing, forming unsafe ice patches.
In 2024, Gradient also carried out two more pilot studies—the first a 100-unit pilot project in California’s Central Valley, funded by the California Strategic Growth Council. They deployed units in both multi-family and single-family low-to-medium income homes. The project aimed to assess the performance, installation process, and user satisfaction of the window heat pumps in diverse settings. The second was a field trial using five of Gradient’s units in the Pacific Northwest, funded by the NEEA. This focussed on DIY installation and usage patterns demonstrating the practicality and user-friendliness of Gradient’s heat pumps in residential settings. They have a few more pilot projects being negotiated right now, including another order for multiple thousands of units.
Gradient’s product has been recognised several times, including the 2024 Integrated Home Competition Grand Prize from the Consortium for Energy Efficiency (CEE), and Energy Star certification—the highest possible classification of energy performance.

How they have scaled their production
Gradient has a team of around 45 employees, and they do all their research and design in-house. Early on, they decided to work with manufacturing partners, as the materials, components, processes and skills required are similar to those found in other HVAC units. Replicating this in-house would be slow and expensive, and unlikely to form a source of competitive advantage, so this represented the quickest path to produce quality units at scale. Gradient collaborate with multiple suppliers to make individual components, from sheet metal to printed circuit boards (PCBs). After early issues with supply chain reliability they have proactively partnered with a leading HVAC manufacturer for more reliable product availability. They work with a separate contract manufacturer to make custom plastic components using injection moulding. The core of Gradient’s system, the heat pump, involves joining several components including the compressor, heat exchangers, expansion valve and reversing valve with copper tubing using a kind of welding called brazing. This has been done in-house for early prototypes, but now the assembly is performed by another partner to facilitate scaling. The system is filled with the R32 refrigerant and then undergoes rigorous testing. The final assembly of the heat pump with the housing, PCB and wire housing resembles a small automotive production line. After final testing, the units are packed and shipped to customers, who download an app to customise their settings and access support.

How have they funded their growth
Gradient has successfully secured several rounds of equity investment to support its growth and innovation. In 2023, they raised a $27.5M Series A, led by Climate Investment, and joined by Collab Fund, Course Corrected Capital, Sustainable Future Ventures, and AtOne Ventures. The funds are intended to enhance product development, expand operations, and accelerate the adoption of their heat pump technology. Prior to this, Gradient had secured more than $13 million in venture funding, including backing from Elemental Impact, Sustainable Future Ventures; and over $9 million in non-dilutive grants and awards, including awards from the Department of Energy.
Want to find out more? Gradient have been featured by Wired, Fast Company, The Verge, Slate, and Bloomberg. You can follow Vince and Gradient on LinkedIn and the Gradient website.
Case study 3: Lilac - Direct lithium extraction (hybrid route)
How It Started

Lilac Solutions was founded in 2016 by Dave Snydacker, a materials engineer with a Ph.D. from Northwestern University. Snydacker’s expertise in battery technology and his commitment to addressing climate change led him to develop innovative methods for lithium extraction. Identifying limitations in traditional extraction techniques, he established Lilac Solutions in Oakland, California, to pioneer more efficient and environmentally-friendly processes. Pippa met Dave at the pitch session of the Verge conference in 2017 (video), and made an angel investment soon after.
How It’s Going
Lilac Solutions has developed a proprietary ion exchange (IX) technology designed to enhance lithium production from brine resources. This method offers higher efficiency, reduced costs, and a significantly smaller environmental footprint compared to conventional techniques.
The company’s technology has been implemented in various pilot and demonstration projects:

2023 Kachi Project in Argentina (completed): In collaboration with Lake Resources, an Australian responsible lithium developer, Lilac deployed its IX technology at the Kachi Lithium Brine Project. The demonstration plant achieved high purity lithium (>99.8%) high lithium recovery rates with minimal water usage, marking a pivotal step toward commercial-scale operations (video).
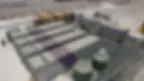
2024 Atacama Field Pilot in Chile (completed): Lilac successfully completed a field pilot in the Atacama region, achieving 94% lithium recoveries on brines with lithium concentrations of 2,200 mg/L using its Gen 2 IX technology.

2024 Jujuy Demonstration in Argentina: The company conducted a demonstration project in Jujuy, processing brines with lithium concentrations of 324 mg/L using its Gen 4 IX technology.
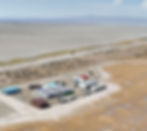
2024 Great Salt Lake demonstration project: hiding in plain site is the Great Salt Lake in Nevada, full of lithium but at low concentrations (60mg/L) and with contaminant levels previously not viable for extraction. Lilac have installed a pilot project in current operation demonstrating the ability of their technology to recover 65% of the lithium, returning all the water to the lake with no charge in the chemistry aside from the removal of the lithium.
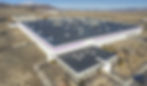
How they’ve scaled their production
Lilac have pursued a hybrid approach with a central FOAK + modular process units for
pilots.
The core of their technology, the ion exchange resin beads, have always been produced in-house to safeguard their intellectual property, and to establish an additional defensive moat with the associated know-how for production. Initially, the beads were made in small batches in their Oakland lab; and then in 2020 they successfully expanded their bead manufacturing to pilot scale to produce the material for pilots globally. In 2024, they started work on a proprietary FOAK bead manufacturing plant in Nevada.
The balance of their plants is the equipment needed to get the brine in and out of the beads. Lilac has developed a containerised system to power feasibility studies and pilot projects, using shipping containers which are designed, engineered, and fabricated at their headquarters in Oakland before being shipped to site. Each pilot has multiple containers hosting the process units, which handle the brine filtration, reagent preparation, lithium extraction and water recovery, These are paired with a central controls container which does all the monitoring and controlling required. Once a pilot project is completed, the whole system can be shipped to a new site. Although most of this equipment is off-the-shelf, by creating a proprietary modular mobile system for pilots, Lilac maintains control over processes and IP relating to the system - and can reuse, reducing costs and deployment time.

For larger demonstrator and commercial-scale projects, the same technology is scaled up and situated in warehouses:
How They Funded Their Growth
Lilac Solutions has raised over $300m in VC funding, as well as grants and project financing. In 2018, they started with a seed round filled with angels and aligned impact investors PRIME Impact Fund. This was followed with $20M Series A funding in 2020 from Breakthrough Energy, The Engine and Lowercarbon Capital, and a $150M Series B in 2021 led by T. Rowe Price joined by previous investors. In 2024, Lilac closed a $145 million Series C round led by energy and commodities corporate Mercuria and joined by previous investors, bringing its total capital raised to $315 million. They have also benefited from multiple non-dilutive grants and awards, including a $50M grant from the U.S. Department of Energy’s Office of Manufacturing and Energy Supply Chains (“MESC”) and Office of Energy Efficiency and Renewable Energy (“EERE”) to advance domestic lithium production. For project financing, they have worked with strategic partners who have supplied capital to demonstration projects, and they have received revenues from customers commissioning pilot projects and feasibility studies. Lilac now has 200 employees.